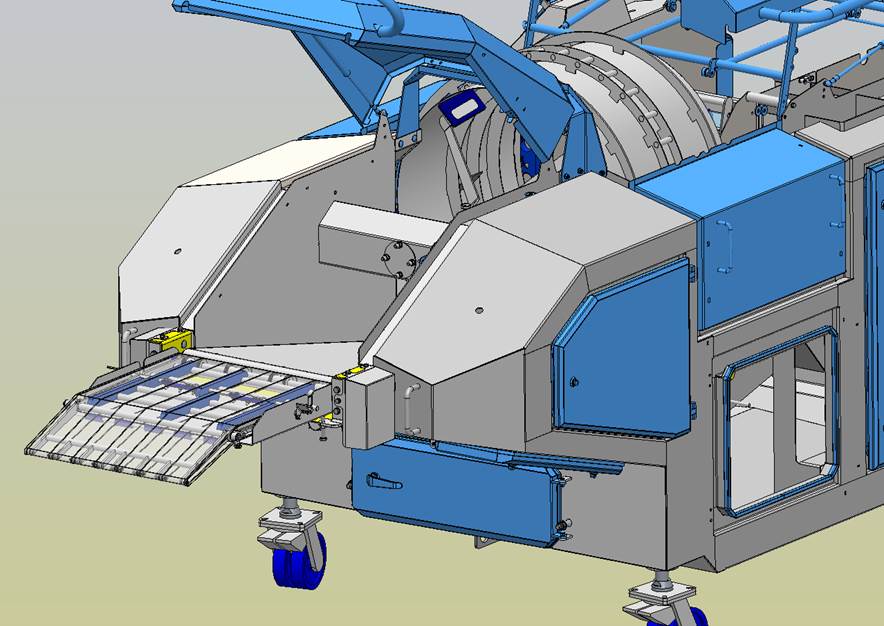
The first product Symotab brought to the market is Combi Coater, a drum and flatbed applicator for dry ingredients. The Combi Coater was designed from the ground up in the Netherlands by VDL systems in Uden. The company VDL systems is part of one of the largest industrial conglomerates in the Netherlands.
The first prototype Combi Coater came out in February 2017 and was tested and updated multiple times before the first order was signed in December 2017.
The idea to bring Combi Coater to the market was that there is to date no metric European made breader on the market that can work with flour and crumb on the identical machine and can work as drumbreader, also as flatbed preduster and as flatbed breadcrumb applicator.
Inspiration:
Further inspiration came from the success of a tablet and phone manufacturer. Their success showed that complex processes, when visualised with pictures and icons made it easy and fun to manage them.
Combi Coater has 9 frequency drives and connected motors on board but not a word of any language in the HMI for operators. The motors are shown as pictorial icons where operators can click on and then set the desired speed as a percentage of the maximum. In practice it gives operators a good sense of control over how the products enter and exit.
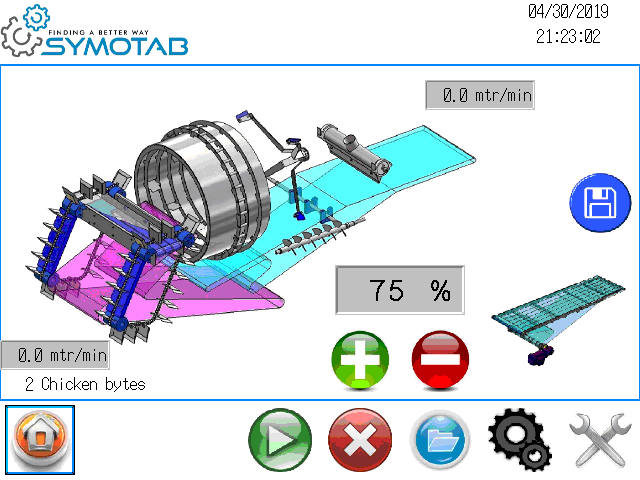
Operational costs:
An important attention point is that convenience lines are costly to operate. Usually products that have a core temperature of around -2 to +4 degrees will typically be heated to a core of 72-80 degrees and then IQF frozen to a core of -18 Celsius all in one continuous pace. The energy that is needed for this process + the cost of employees needed on the line and in the packaging area represent usually a cost 4.000 – 5.000 EURO per hour. Coating machines usually count for the majority of production stops on lines where high pickups are realized.
Designed with ruggedness:
Combi Coater is designed with ruggedness in mind and such that almost all spareparts can be sourced locally. That way there is no waiting time for overseas supplies for example and vulnerability of depending on the supplier of the machine of your choice. Only parts from the best suppliers are used such as motors and gearboxes from SEW, electronics from Rockwell and Schneider.
The drive systems are designed around optimizing the traction to prevent slippage. For example, the infeed belt responsible for large quantities powder transport, covers the drive sprockets by 270 degrees securing a smooth run under heavy conditions.
Please check out CombiCoater.com for more detailed information and leave a comment in the comment section.
How can I help you?
Ad Bontje,
Ad@symotab.com